Felss Systems GmbH is a machine building and process engineering company and part of the Felss Group. Felss Systems is an automotive supplier as well as a specialist in cold forming processes of tubes applying rotary swaging, axial forming, bending, autofrettage and tube end forming.
To stay ahead of the pack in this highly competitive industry, internal processes need to be integrated into interconnected systems. Felss Systems chose X-INTEGRATE’s specialized, custom-made solution to their challenge. Predictive scoring and automation were the keys to significantly increasing the efficiency of industrial machines who use highly precise forming-process technology.
The predictive analysis method that was put in place starts with sensors placed on the machines in the production line. They constantly measure and monitor the quality of the machines and the parts they make. The goal of this is to continuously collect valuable, meaningful data which enables accurate predictions when it comes to the quality of the manufactured parts. On top of that, the solution also facilitates reacting with flexibility if there are any occurrences and it makes the process of changing machine components much more efficient.
Within the automotive supplier industry there is great pressure to keep increasing the efficiency of internal processes and to stay abreast of the changes industry 4.0 is bringing with it. The perfect spot to hook into when it comes to optimizing efficiency is anything related to processes requiring much personnel, like component changing, set-ups and quality controls. These all require a lot of time and resources. To keep Felss Systems and its customers competitive, custom-made solution needed to be found for those processes.
The method X-INTEGRATE came up with heralds a paradigm shift in the billion-dollar automotive and forming-process industry. Up until now, the gold standard was the direct measuring of physical dimensions and the direct attribution to physical effects.
The solution we devised with Felss Systems, however, is based on indirect measuring and an accompanying intelligent analysis of the results. X-INTEGRATE developed a predictive analytics method that improves the quality management of products as well as that of the machine components making them. Traditional inspection intervals are replaced by a constant scoring process, which includes predictive capabilities based on IBM SPSS. This gets placed on an edge gateway that supports industry connectivity standards, which is then installed locally on to the machines of the production line. Taking into consideration various operation-relevant measurements, such as pressure and strength, precise predictions can be made about the condition of the machines and the quality of the parts they are producing. Mathematical methods and, among other things, neural networks help to indirectly check the machine components which are known, from previous experience, to be susceptible to quality problems.
The customary inspection intervals are replaced by a so-called scoring process, which has a much greater accuracy in predicting when the next technical maintenance needs to be performed. The machinist gets a visual notification right at the affected machine, before any malfunctions or failures can occur during the production process.
The enrichment of their machines and products with predictive analytics functions gives Felss Systems an edge over competitors in their main sales market: the automotive industry. The new, much more precise inspection capabilities make it easier to predict when there will be a drop in quality along the production line and when components need to be replaced. This in turn helps planning, ordering and executing replacements in a flexible way, in realtime.
The risks of machine failures or deficient products are minimized. Quality control processes requiring a lot of manpower are now made more efficient and automated by logging and saving everything in a database – from the tracing of data over the predictions made by the SPSS model to the ensuing reports. Due to this documentation and self-learning system, processes will continuously be optimized up until, at some point in the future, the machines’ profiles will self-adjust automatically.
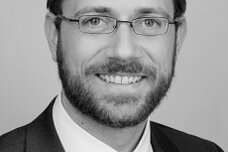
„Up until now, the gold standard was the direct measuring of physical dimensions and the direct attribution to physical effects. The solution we devised with X-INTEGRATE, however, is based on indirect measuring and an accompanying smart analysis of the results that yields highly reliable data.“
Dr. -Ing. Dipl. -Wirt.-lng. Michael MarréHead of Engineering and InnovationFelss Systems GmbHThe pressure to increase efficiency when building and running production line machines is enormous these days. Companies can get ahead of the competition if they streamline their internal processes and convert to industry 4.0.
The more they rely on predictive planning and automated processes, the more efficient their production capabilities become. Especially areas like maintenance and quality control use a lot of personnel and thus hold a lot of optimization potential. Both take up a lot of time and resources: at set, regular intervals parts have to be retrieved from the production line and checked in a time-consuming process.
The need for checks and the sensible choice of intervals are challenging: if the intervals are too short, unnecessary and expensive delays in production are the result; if the intervals are too long, deteriorated components are only discovered once there are malfunctions.
Predictive Analytics-Software to optimize maintainance processes
This is where the predictive analytics method which X-INTEGRATE’s experts developed for Felss Systems comes in. In its capacity, among other things, as an automotive supplier, Felss uses machines that form metal for transmission shafts, steering shafts, propulsion components and many more highly specialized parts.
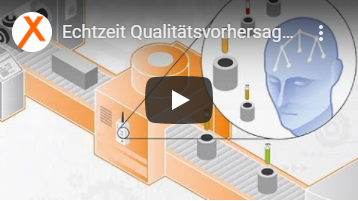
The expectations about fast, flexible processes are especially high when it comes to producing extremely precise, high-quality interlocking parts. To ensure this, the traditional inspection intervals were scrapped in favor of a constant scoring process, based on a prediction model by IBM SPSS.
The first step was to install sensors on the machines. Their data is collected in an edge gateway that supports industry connectivity standards. The predictive analytics software by X-INTEGRATE then reads out the relevant information and compares the sensors’ data with the standards the machine should be running on, for instance correct pressure or temperature. It’s programmed to only check components where there is a known risk of deterioration over time. Then, a prediction is made as to the possible condition of the deficient component. The results are sent back to the machine via an integration component and they show up for the machinist in charge.
Dynamic, realtime performance in crucial here, since production lines operate on a second-by-second basis and so the answer time of the predictive process – from measuring over the SPSS’ prediction to the sending of a notification to the machine – needs to lie within that timeframe as well. This method is a true paradigm shift within the billion-dollar automotive and forming-process industry.
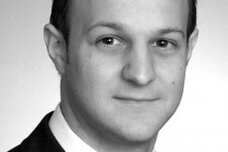
„While developing this monitoring system, the scalability of it, as it would apply to various customers, was of the utmost importance to us. That scalability is achieved through a scoring software that can be trained. The new predictive model will guarantee to our customers that no deficient parts can end up in further manufacturing processes, for instance they will never get installed into any car.“
Dr. Matthias KlugeLeader for tool and forming-process technologyFelss Systems GmbHThe process of creating a reliable and solid prediction model
Thanks to continuous, precise checks production managers can more reliably predict when certain machines in a production line will need maintenance or adjustment and plan accordingly. Customers of Felss Systems can switch off, repair affected machines, or change worn down tools long before a critical point is ever reached.
Within the production line, that translates to fewer wasted products and much smaller chances of suffering an unexpected machine failure. Quality control of the parts produced also becomes exponentially more efficient because of the predictive analytics method used.
Quality control processes requiring a lot of man-power are now made more efficient and automated by logging and saving everything in a database – from the tracing of data over the predictions made by the SPSS model to the ensuing reports. That also contributes to the continuous improvement of the predictive model.
Felss Systems can now tap into a new field of business with a managed services package of its industry 4.0 machines. The scalability of the solution paves the way to an intelligent factory, for Felss Systems and all of its customers, past, present and future.
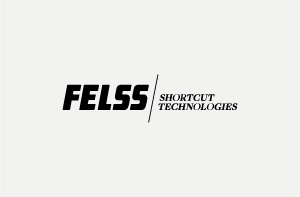
About Felss Systems GmbH:
Under the brand name Felss Shortcut Technologies, the Felss Group produces both metalworking machines and components for various industries, such as the automotive industry.
The technical focus is on the cold forming processes rotary swaging, axial forming, bending and end machining. Headquartered in Königsbach-Stein, Felss generates over 122 million euros with approx. 630 employees in 5 countries.
The innovative company has received several awards in recent years for its novel products in the Industry 4.0 sector and for its commitment to resource-efficient manufacturing.
- Branch: mechanical engineering
- Employees: > 500
- Reach: international